Success story
Roxtec’s change management process made work easier for the employees
Roxtec's product development relies on the PLM platform Teamcenter from Siemens Digital Industries, which manages master data about the products and is connected to their CAD systems AutoCad and Inventor as well as to their business system IFS. Since the implementation of Teamcenter 2014, Roxtec has been further developing processes and procedures to ensure the quality of its product data.
Main success factors
Dedicated project team
Main benefits
High data quality
Extensive time savings
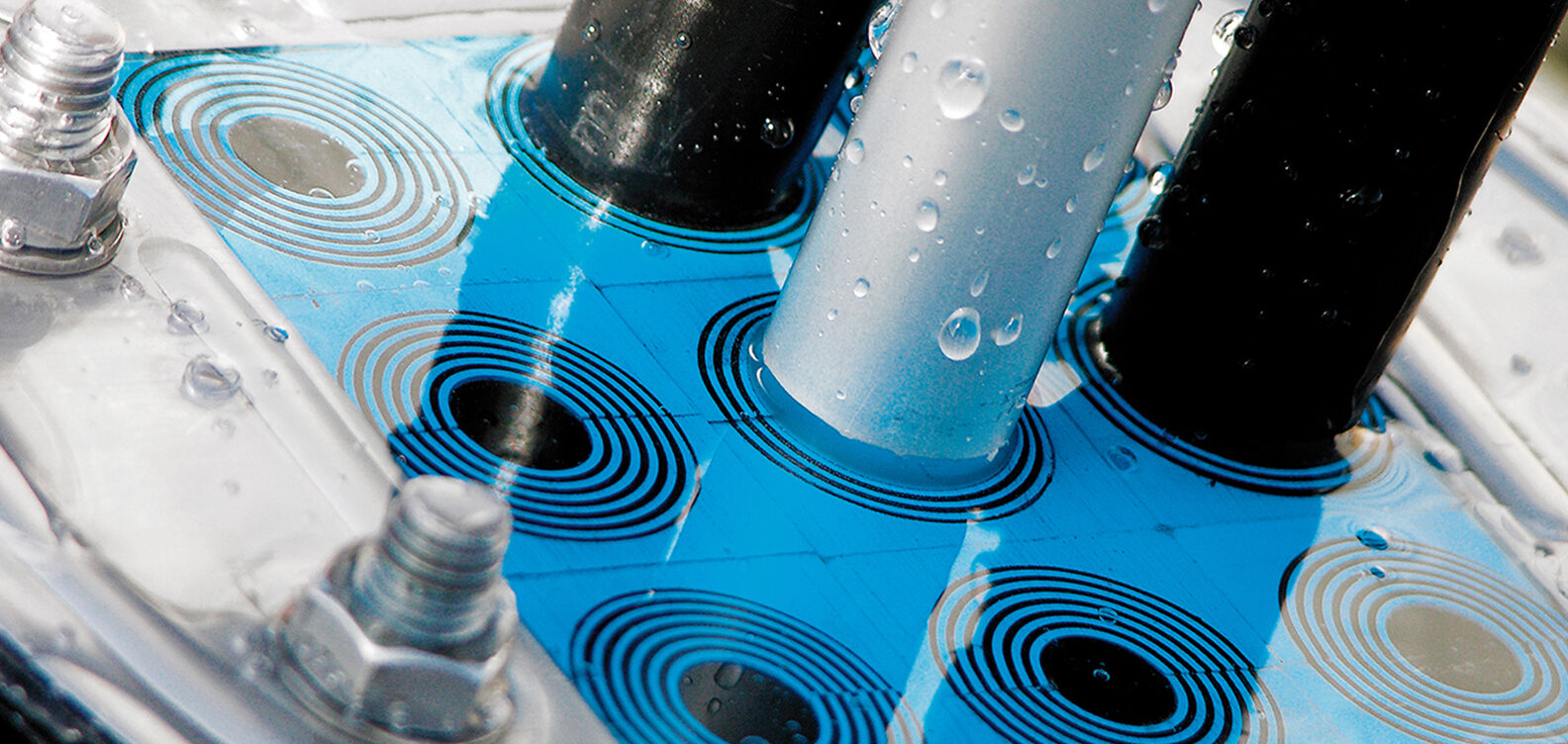
Roxtec has secured its delivery quality and made significant time savings by implementing a change process with system support in Teamcenter
Roxtec develops, manufactures and sells complete sealing solutions for cable and pipe penetrations. They have customers in all industry sectors where pipes and cables need to be safely drawn through different types of materials, on land, at sea or underground and they have both standardized and customized solutions. The Karlskrona-based company has seen strong growth over the years and today has over 800 employees spread over 28 companies around the world.
Roxtec’s product development relies on the PLM platform Teamcenter from Siemens Digital Industries, which manages master data about the products and is connected to their CAD systems AutoCad and Inventor as well as to their business system IFS. Since the implementation of Teamcenter 2014, Roxtec has been further developing processes and procedures to ensure the quality of its product data.
Ronnie Pettersson is Design Engineer at Roxtec:
“After the implementation of the ECR process, we see higher quality in our product data which contributes to higher quality customer delivery, major time savings and better control of our products and manufacturing.
The benefits are felt by all Roxtec employees involved in the product life cycle, from designers and product processors to procurement/logistics, production and service.”
The background
The positive growth with increased number of subsidiaries and employees placed new demands on the organization. The delivery rates and complexity increased, making structured information transfer more important. Roxtec noticed that the delivery suffered due to the different methods for handling the documentation of changes to products in different parts of the company. They lacked process and system support. Employees spent time searching for and validating change information that affected procurement, manufacturing and delivery.
Since 2014, Roxtec has had support for Engineering Change Notice (ECN) in connection with the implementation of Teamcenter. To ensure delivery quality, in 2016 Roxtec started looking at an extended Engineering Change Request (ECR) process and at the possibility of integrating it with its business system. The new Change Management process was implemented in 2017 and is supported by Nextage’s Teamcenter solution. The result was full searchability, traceability and control of changes throughout the entire life cycle of the product, and as a consequence — more satisfied employees.
Andreas Krantz is Product Owner at Roxtec:
“Change Management is a process and a way of working, but in order to succeed it is important to have competent system support.
The project
The work on describing Roxtec’s Engineering Change Request process was driven by seven people from different key departments, including strategic and operational procurement, design, and finance. The assignment was to create a well-functioning process that focused on people and systems, and would contribute to higher quality of the product documentation. The aim was to ensure the searchability and traceability of all changes throughout the entire life cycle of the product.
Roxtec’s solution in Teamcenter has a product-centered information model. This means that the product is the cohesive node for all relevant information, including information about changes. The solution also supports decision-making on changes through a predefined regulatory framework.
Objects for changes are added to Teamcenter and contain the following information:
- Description of the change
- What needs to be done
- When the change needs to be implemented
- Impact on the product and links to other objects
- Which new objects have been created as a result of the change
The process is designed to support all types of changes. Minor changes with a few recipients can be initiated and completed within one hour, while major ones can take several months and involve a larger group of participants.
Early in product development, changes occur continuously. One issue that came up was at what stage of the design process a change should be classified and formally treated as a change.
Roxtec considered that when the product is available to the customer, changes should be managed in the ECR flow.
The design engineers and change management
The design engineers at Roxtec work in Teamcenter every day. Teamcenter is integrated with their two CAD systems Inventor and AutoCAD.
When the ECR process was introduced it initially felt like extra work to add information about changes to the system. Soon they saw the benefits of the process.
Ronnie Pettersson is Design Engineer for customized solutions. He has been involved both before and after the implementation of the new CM process. A background is now always provided as to why a change is being considered. Roxtec’s engineers specify the advantages and disadvantages of the change which are included as a basis for decision-making. It is a simple and fast process where references such as customer documentation or email can be added. In the next step, product preparation can add information they have received via the business system.
Ronnie Pettersson explains:
“The Change Management process documents what changes we have made and why. Traceability helps us a lot. Another great advantage is that automated flows provide information to the right people about how the product has been changed, thereby facilitating handover. Previously, I had to export information from the CAD system and email it or share it in some other way. In addition, I often had to hunt people by phone to make sure they have received and understood the information.”
Integration with the business system with Teamcenter as master
The integration between Roxtec’s business system and Teamcenter is carefully thought out and governs which information should be transferred to which part of the ERP system. Part numbers are only created in Teamcenter and then pushed over to the business system. Some fields are locked in the business system, which helps maintain high-quality product information.
Roxtec’s business system users immediately saw the benefits of the new change process, which saved a lot of time in finding and validating information about product solutions. In addition, they now had a master — a common way of working with subcontractors and subsidiaries, and the information available in the system is what applies. It provides both overview and control.
Today, everyone works according to the same process where Teamcenter is the master of all product information, including changes. Automated flows ensure that the right change information is sent to the right person at the right time. Employees do not need to spend time validating changes.
Marita Lindberg works with Product Preparation at Roxtec:
“The process is a great support. Knowing that the information is correct facilitates our work. We also save a lot of time on the process as instead of creating new part numbers, we can now make changes to an existing product.”
Benefits for the Roxtec team
After the introduction of process and system support in the form of Teamcenter Change Management, changes and information now flow smoothly between functions, subsidiaries, and manufacturing in Roxtec.
The coworkers describe how the processes benefit them in their daily work.
Ronnie Pettersson, Design Engineer, Roxtec
“After the implementation of the ECR process, we see a higher quality in our product data which contributes to higher quality customer delivery, major time savings, and better control of our products and manufacturing. The benefits are felt by all Roxtec employees involved in the product life cycle, from designers and product processors to procurement/logistics, production, and service.”
”The data model in Teamcenter provides a clear overview. All information relating to the product, including changes, is neatly lined up in front of me as the user when I open it. Teamcenter supports all types of documentation such as email, PDF, images, etc. I no longer have to search in long email threads, which makes it easier for me to do the right thing and saves a lot of time.”
Jens Bohlin, Technical Project Manager, Roxtec:
“To me personally, in my daily work, time savings became the most obvious benefit after the introduction of the Change Management process in Teamcenter.”
Roxtec’s top tips on implementing change management support
- Make sure the change process facilitates work for the users
- Keep business benefits in mind at all times
- Allow the process to mature and introduce changes in rounds
- Keep in mind that the process is not locked in the system, but can be further developed in a way that is economically and systemically sustainable.
- Continue to remind and train staff on why the process is important
Simplicity
Simplicity in seeing which items and what aspects of manufacturing or procurement are affected by a change.
Clarity in which people and functions need to be involved in each process— from engineering to procurement, supply-chain and manufacturing process and customers Simplified distribution of information — the right information to the right person at the right time.
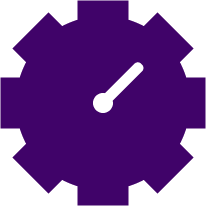
Productivity
Automated activities save time. Changes reach the right people, and are no longer person-dependent or manual, but are handled by the system.
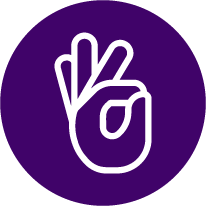
Quality
Thanks to the full traceability and history of each product and article Roxtec experiences increased data quality, and hence: increase delivery quality.
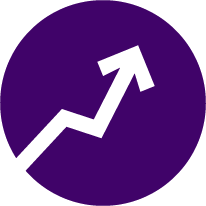
Profitability
In the end, time-saving, fewer mistakes late in the manufacturing process, and a higher data quality overall lead to higher profitability.
Roxtec’s operations expanded and sales steadily increased. Our subsidiaries, as well as the parent company’s productivity and sales, led to an increased need for process and system support in order to continue to grow while maintaining control and quality. Support in Teamcenter helps us succeed.
Jens Bohlin, Technical Product Manager
Roxtec
Roxtec develops, manufactures, and sells complete sealing solutions for cable and pipe penetrations. They have customers in all industry sectors where pipes and cables need to be safely drawn through different types of materials, on land, at sea, or underground and they have both standardized and customized solutions. The Karlskrona-based company has seen strong growth over the years and today has over 800 employees spread over 28 companies around the world.
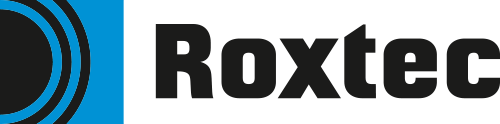

Accelerate your business
Follow us on LinkedIn